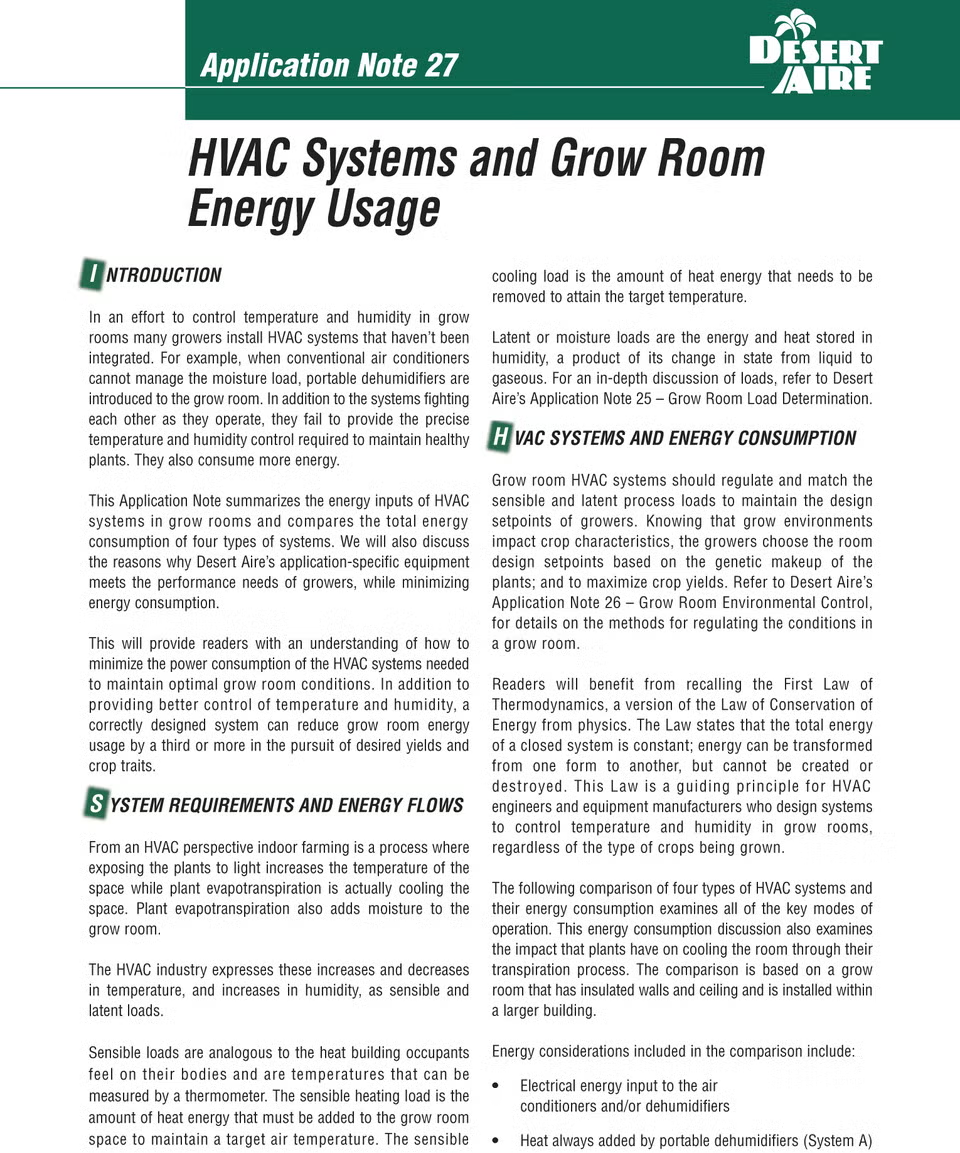
HVAC Systems and Grow Room Energy Usage | AN27
This Application Note summarizes the energy inputs of HVAC systems in grow rooms and compares the total energy consumption of four types of systems. We will also discuss the reasons why Desert Aire’s application-specific equipment meets the performance needs of growers, while minimizing energy consumption.
Gated Content Overview Headline Default
Lorem ipsum dolor sit amet, consectetur adipiscing elit, sed do eiusmod tempor incididunt ut labore et dolore magna aliqua.
Gated Content
Please fill out the form for access.
Overview
In an effort to control temperature and humidity in grow rooms many growers install HVAC systems that haven’t been integrated. For example, when conventional air conditioners cannot manage the moisture load, portable dehumidifiers are introduced to the grow room. In addition to the systems fighting each other as they operate, they fail to provide the precise temperature and humidity control required to maintain healthy plants. They also consume more energy.
This Application Note summarizes the energy inputs of HVAC systems in grow rooms and compares the total energy consumption of four types of systems. We will also discuss the reasons why Desert Aire’s application-specific equipment meets the performance needs of growers, while minimizing energy consumption.
This will provide readers with an understanding of how to minimize the power consumption of the HVAC systems needed to maintain optimal grow room conditions. In addition to providing better control of temperature and humidity, a correctly designed system can reduce grow room energy usage by a third or more in the pursuit of desired yields and crop traits.
System Requirements And Energy Flows
From an HVAC perspective indoor farming is a process where exposing the plants to light increases the temperature of the space while plant evapotranspiration is actually cooling the space. Plant evapotranspiration also adds moisture to the grow room.
The HVAC industry expresses these increases and decreases in temperature, and increases in humidity, as sensible and latent loads.
Sensible loads are analogous to the heat building occupants feel on their bodies and are temperatures that can be measured by a thermometer. The sensible heating load is the amount of heat energy that must be added to the grow room space to maintain a target air temperature. The sensible cooling load is the amount of heat energy that needs to be removed to attain the target temperature.
Latent or moisture loads are the energy and heat stored in humidity, a product of its change in state from liquid to gaseous. For an in-depth discussion of loads, refer to Desert Aire’s Application Note 25 – Grow Room Load Determination.
HVAC Systems And Energy Consumption
Grow room HVAC systems should regulate and match the sensible and latent process loads to maintain the design setpoints of growers. Knowing that grow environments impact crop characteristics, the growers choose the room design setpoints based on the genetic makeup of the plants; and to maximize crop yields. Refer to Desert Aire’s Application Note 26 – Grow Room Environmental Control, for details on the methods for regulating the conditions in a grow room.
Readers will benefit from recalling the First Law of Thermodynamics, a version of the Law of Conservation of Energy from physics. The Law states that the total energy of a closed system is constant; energy can be transformed from one form to another, but cannot be created or destroyed. This Law is a guiding principle for HVAC engineers and equipment manufacturers who design systems to control temperature and humidity in grow rooms, regardless of the type of crops being grown.
The following comparison of four types of HVAC systems and their energy consumption examines all of the key modes of operation. This energy consumption discussion also examines the impact that plants have on cooling the room through their transpiration process. The comparison is based on a grow room that has insulated walls and ceiling and is installed within a larger building.
Energy considerations included in the comparison include:
- Electrical energy input to the air conditioners and/or dehumidifiers
- Heat always added by portable dehumidifiers (System A)
- Cooling of the enhanced dehumidifier with heat exchanger (System B)
- Cooling of the grow room zone via plant transpiration
- Heat required to overcome lights-off transpiration (Systems A, B, C)
The HVAC energy profile of a grow operation has two elements to consider. The room may have outdoor energy loads known as building thermal loads. This could be the heat gain during the summer months and heat loss during the winter. The second element is the load caused by the growing process. This includes the lighting heat gain as well as the moisture from the plant watering.
We will be reviewing four types of typical systems as summarized below.
- System A – Conventional Air Conditioning with Supplemental Portable Dehumidification Units
- System B – Conventional Air Conditioning with Enhanced Dehumidification
- System C – Conventional Air Conditioning with Split Dehumidification Systems
- System D – Desert Aire GrowAire™ Environmental Control System
Large Plants | Emergent Plants | |||
Type | Sensible Cooling Btuh | Latent Dehum. lb/hr | Sensible Cooling Btuh | Latent Dehum. lb/hr |
Building Load – Summer | 55,000 | 24 | 55,000 | 24 |
Lighting | 444,000 | – | 444,000 | – |
Evaporative cooling effect of plants | (117,000) | 110 | (70,000) | 66 |
Total lights on sizing loads | 382,000 | 134 | 429,000 | 90 |
System A – Conventional Air Conditioning with Supplemental Portable Dehumidification Units
The air conditioner in System A is sized to handle the entire sensible cooling load and will remove a portion of the moisture during the lights-on mode. The supplemental portable dehumidifier uses an internal hot gas reheat coil to reject all of the collected energy and is sized to remove all of the moisture in the lights-off mode. The dehumidifier supplements the work of the air conditioner in the lightson mode. When in operation the leaving air temperature of the dehumidifier is 25°F warmer than when it entered, thus adding heat to the space. This heat load must be removed either by the evapotranspiration process or the air conditioner.
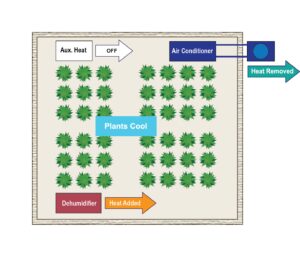
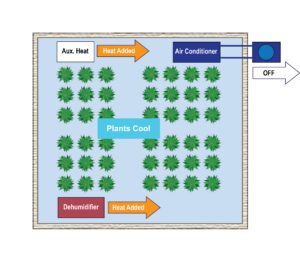
System B – Conventional Air Conditioning with Enhanced Dehumidification
System B is an alternative method that uses a dehumidifier containing heat exchanger plates or heat pipes to improve the moisture removal capacity of the unit. This upgraded system removes more moisture per kilowatt of input power. The dehumidifier achieves the incremental improvement by reheating the leaving air after the plate or heat pipe in a step commonly called “free reheat.” This is a fixed system that cannot change the temperature of the leaving air, thus requiring additional air conditioning for lights-on cooling or additional auxiliary heat for lights-off heating.
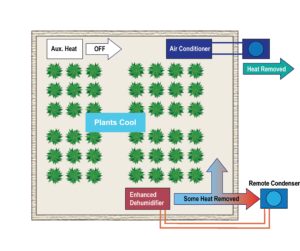
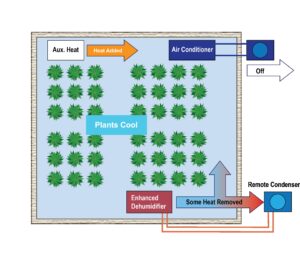
System C – Conventional Air Conditioning with Split Dehumidification System
The baseline for System C is a conventional split system air conditioner and a split dehumidifier that has a remote air-cooled condenser. This remote condenser provides additional cooling as compared to only having the internal hot gas reheat function of portable dehumidifiers. In the lights on mode, the dehumidifier more effectively removes moisture while also cooling the space.
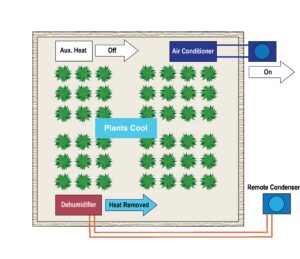
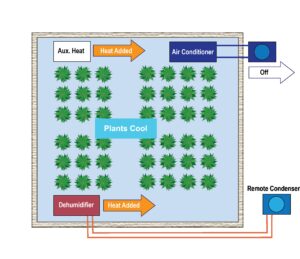
System D – Desert Aire GrowAire™ Environmental Control System
Desert Aire’s GrowAire™ Environmental Control System is an integrated solution that performs the work of the conventional air conditioner and the dehumidifier by using controller logic to modulate sensible heat ratios. This controller logic enables the system to remove heat or add it back into the space as required during both lights on and lights off cycles.
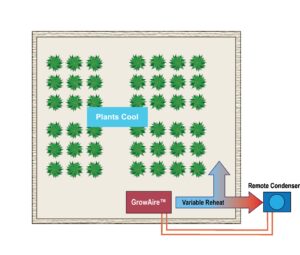
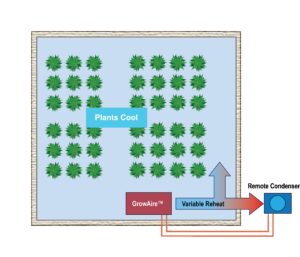
Annual Operating Costs
The performance factors for the various types of equipment are summarized in Table 2 below and normalized per nominal ton. The air conditioning system is based on a highly energy efficient design of 16 SEER and the portable dehumidifier complies with the latest AHAM rating of 2.7 liters per kWh. Performance data was established for each equipment manufacturer performing at a 75°F/50% RH condition.
Sens. Clg. | Latent Dehumidification | Latent Operational | ||
Type | Btuh | Btuh | lb/hr | kW |
Air Conditioner | 8,100 | 3,600 | 3.4 | 0.72 |
Portable Dehumidifier | (8,300) | 4,200 | 4.0 | 0.85 |
Enhanced Dehumidifier | 7,800 | 4,500 | 4.2 | 0.63 |
Split Dehumidifier w/ clg | 1,600 | 6,000 | 5.7 | 0.68 |
GrowAire™ System | 8,000 | 4,600 | 4.3 | 0.70 |
Table 3 displays the estimated annual operating costs for the four systems outlined above, based on an electricity cost of $0.12/kWh. The table is based on a grow room with a crop canopy area of 2,600 square feet and a watering rate of 0.5 gal./day/plant (0.15 gal./day/sq. ft.). The lighting load was based on 50 watts/sq. ft. with the lights on and a fully developed canopy. The table was created by calculating the loads in both the lights on and lights off modes and using the performance of each system type to estimate the energy consumption.
AC w/Additional Systems | ||||
System A Portable Dehumidifier | System B Enhanced Dehumidifier | System C Split System Dehumidifier with clg. | System D GrowAire™ Environmental Control System | |
Lights ON | ||||
Air Conditioner (kWh) | 67 | 53 | 46 | – |
Dehumidifier (kWh) | 24 | 9 | 13 | – |
GrowAire™ System (kWh) | – | – | – | 49 |
Total Energy – Lights ON | 91 | 62 | 59 | 49 |
Lights OFF | ||||
Air Conditioner (kWh) | 0 | 0 | 0 | – |
Dehumidifier (kWh) | 24 | 13 | 18 | – |
GrowAire™ System (kWh) | – | – | – | 16 |
Extra Heat Required (kWh) | 0 | 28 | 0 | 0 |
Total Energy – Lights OFF | 24 | 42 | 18 | 16 |
Totals | ||||
Annual kW/sq/ ft. Consumed | 115 | 104 | 77 | 65 |
Electrical Costs Per Year/sq. ft. | $13.80 | $12.48 | $9.28 | $7.80 |
Annual Energy Cost | $35,892 | $32,452 | $24,140 | $20,284 |
Reduction in Annual Energy Costs From System A | – | 10% | 33% | 43% |
Impact of Building Envelope
The above analysis is based on a grow room that has an insulated ceiling and walls and is installed within a larger building. If the grow room has exterior walls the heat gain and heat loss through the walls must be included in the room’s load calculations. The heat gain/loss information must be provided by a qualified engineer to ensure proper equipment sizing.
The system examples provide a relative operational cost per square foot of plant canopy and thus provide a scaling factor to compare any grow room. The watering or irrigation rate that each grower utilizes is a key variable as this is the prime driver for the humidity load in the zone. Figure 9 provides a summary of the energy expended per square foot based on the watering rate.
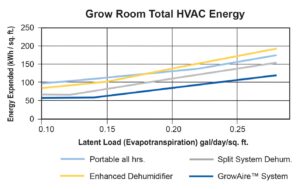
Figure 9 also depicts that different crops and different grow strategies change the watering rate being utilized in each specific application. If the watering load per square foot of canopy or tub space is known, then an estimated total energy comparison can be made for the four different types of systems. Table 4 provides a conversion to a watering rate per plant density based on cannabis plants.
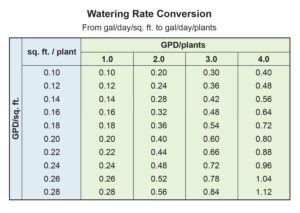
Conclusion
The energy consumption of grow rooms and indoor farms will continue to be an issue not only for the growers, but also for the electric utilities that must provide power to the grow facilities and the surrounding communities.
Desert Aire’s GrowAire™ purpose-built systems combine the functions of air conditioners and dehumidifiers into integrated packages. These engineered solutions provide growers with the lowest operating costs and the tightest temperature and humidity setpoint control available in the industry. GrowAire™ solutions eliminate the supplemental equipment required with other grow room HVAC equipment approaches, thus lowering energy consumption. An additional, critical benefit is the ability to precisely control the vapor pressure deficits of grow rooms. This is a key factor in maximizing crop yields.
Growers, HVAC system planners, utilities and equipment manufacturers need to build on the awareness of the upward sloping energy demands of the grow room and indoor farming industries. In particular there is justification for growers and their HVAC system planners to include utility representatives in the early planning stages of renovation and new construction projects. This inclusive planning approach along with the approximately 40% energy savings of Desert Aire’s GrowAire™ systems should pave the way for growers to receive incentive packages from utilities. This is especially true of utilities seeking to promote resource sustainability and efficiency beyond those merely offering demand-side management rate discounts.
Share or Download
Ask A Question
Related Products

GrowAire™ Series
Desert Aire’s GrowAire™ Dehumidification Systems are specifically designed for indoor farming and ...
View Details
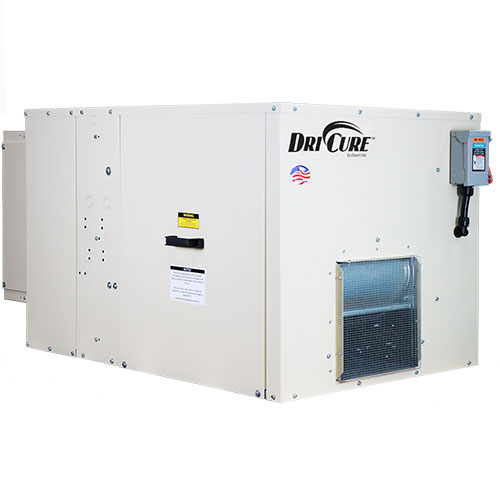
DriCure™ Series Dehumidifier
Desert Aire’s DriCure™ Dehumidification Systems are specifically designed as an all-in-one solutio...
View Details
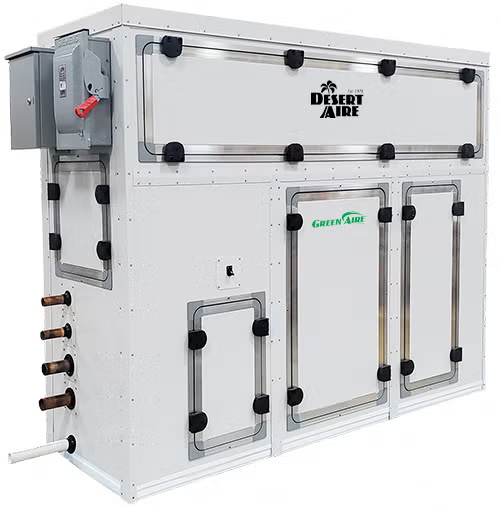
GreenAire™ Series
Desert Aire’s GreenAire™ Dehumidification System offers you complete indoor climate control and su...
View Details
Find a Desert Aire Sales Rep Near You!
Our network of independent representatives are fully trained on Desert Aire’s dehumidification and DOAS solutions and can assist you in designing and sizing your engineered solutions.